Fused Filament Fabrication (FFF)
Material extrusion based 3D printing techniques, such as Fused Filament Fabrication (FFF) and Fused Deposition Modelling (FDM), are manufacturing processes where a solid thermoplastic material is extruded through a hot nozzle. The viscous material solidifies on the build plate which allows build-up of a part with dimensional accuracies typically in the order of 100 μm[1].
The most commonly used thermoplastics for this process are acrylonitrile butadiene styrene (ABS) and polylactic acid (PLA), with typical bulk strengths between 30–100 MPa and elastic moduli in the range of 1.3–3.6 GPa Mechanical properties of 3D printed parts, however, can deviate significantly from the material bulk properties due to the specifics of how a structure is formed on the meso-scale during printing[2].
To maximise the mechanical performance of printed parts, the key elements of the printing process and how they affect final print quality must be understood. Turner et al.4 provide an extensive review on FFF process modelling, including the flow and thermal dynamics of the melt, the extrusion process and the bonding process between successive layers of material. Temperature, viscosity and surface energy of the melt play an important role in how the material flows through the nozzle and more importantly, how the final interface between the beads is formed.
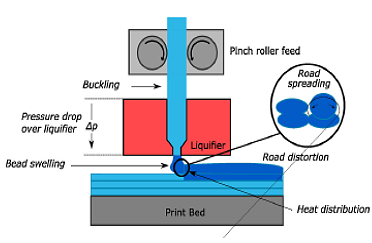
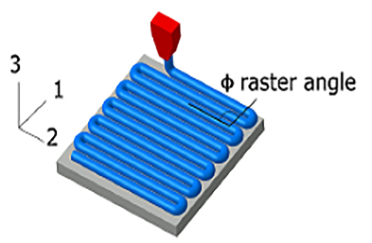
Figure left: Key elements of FFF process
Figure right: Example of meso-structure of 3D printed parts (raster angle)
Selective Laser Sintering (SLS)
Selective laser sintering (SLS) is an additive manufacturing (AM) technique that uses a laser as the power source to sinter powdered material aiming the laser automatically at points in space defined by a 3D model, binding the material together to create a solid structure. SLS (as well as other mentioned AM techniques) is a relatively new technology that so far has mainly been used for rapid prototyping and for low-volume production of component parts. Production roles are expanding as the commercialization of AM technology improves.
SLS involves the use of a high power laser to fuse small particles of plastic, metal, ceramic, or glass powders into a mass that has a desired three-dimensional shape. The laser selectively fuses powdered material by scanning cross-sections generated from a 3-D digital description of the part (for example from a CAD file or scan data) on the surface of a powder bed. After each cross-section is scanned, the powder bed is lowered by one layer thickness, a new layer of material is applied on top, and the process is repeated until the part is completed.
[1] B.N. Turner, S.A. Gold, “A review of melt extrusion additive manufacturing processes: II. Materials, dimensional accuracy, and surface roughness”, Rapid Prototyp. J. 21 (3) (2015) 250–261.
[2] J.F. Rodriguez, et al, "Characterization of the mesostructure of fused‐deposition acrylonitrile‐butadiene‐styrene materials", Rapid Prototyping Journal, Vol. 6 Issue: 3, pp.175-186.